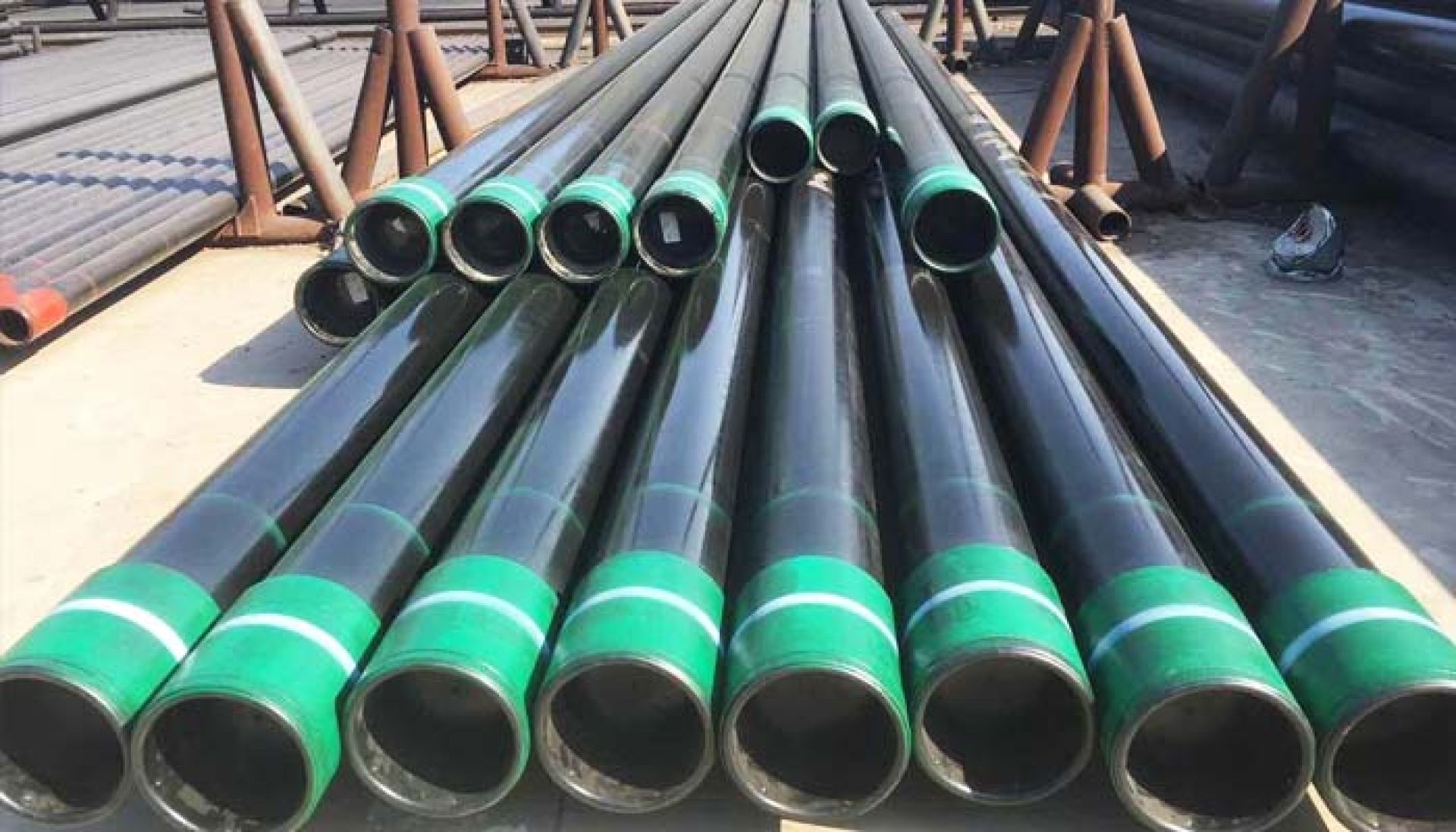
The oil industry is heavily reliant on the innova- tions and products of many other industries, not least that producing something as apparently straightforward as paint.
Throughout the oil production process, protective coatings are critical to safeguard infrastructure, such as pipelines, tanks and refineries, from corrosion, extreme temperatures and environmental degradation.
Moreover, protective coatings enhance safety, reduce operational costs and ensure compliance with industry standards by protecting infrastructure in harsh energy environments. They play a wide range of different roles in the oil industry.
Coatings provide corrosion resistance which prevents metal structures from degrading due to exposure to moisture, salt and chemicals. Fire and heat protection coatings deliver safety-critical insulation in high-temperature processes. Moreover chemical resistant coatings protect surfaces from corrosive spills and splashes.
All in all, the employment of the correct coatings reduces the upkeep costs and prolongs the service life of equipment.
“This minimises maintenance and enhances safety, especially in harsh environments, contributing to a more efficient oil production cycle,” says the chemical engineer Fawzy Ibrahim, Protective Sales Manager of Jotun Libya.
“During the oil production process starting from exploration and drilling, production, separation at GOSP (Gas Oil Separation Plant) until the storage stage, all steel structures require protection against corrosion and environmental deterioration.” he added.
Ibrahim points out that the oil production process is divided into three phases which require a high degree of chemical work running from extraction at the wellhead through to storage at the terminal. In the initial phase, crude oil undergoes preliminary processing to remove water, natural gas, salts and other impurities.
Then comes the transportation of the crude oil via pipelines followed by the final phase which sees the oil delivered to a terminal.
“The floors of the huge oil storage tanks at terminals are exposed over the time to corrosion when water gathers underneath crude oil.
Regarding this, planning and quality control departments at the oil companies usually put plans to conduct maintenance of these tanks, including painting of their floors”, he explains. “This doesn’t occur regularly because emptying the tanks of oil requires a lot of crucial procedures such as reducing or sometimes shutting down of production.”
Painting Types used in the Oil industry.
Many painting companies, including Jotun, have developed a range of innovative protective coating products, especially designed to address the complex needs of industrial and energy sector assets, such as offshore platforms, refineries, pipelines and storage tanks.
One such product is Jotachar, which is specifically designed to shield steel structures in the event of a fire. This kind of painting provides effective protection in hydrocarbon fires and jet fires. It increases the safety and integrity of critical infrastructure in the oil and gas sector. This painting is lightweight and easy to apply, cutting down installation time and cost.
Another coating is Tankguard Special Ultra that offers long-term protection for storage tanks in aggressive chemical environments. This coating is specifically formulated to handle a wide range of chemicals, including many aggressive and corrosive substances used in the energy sector. It gives chemical resistance, especially in environments involving crude oil, refined products and other harsh chemicals. On top of this, it meets strict industry standards for chemical storage, making it a trusted solution for chemical and fuel storage tanks.
There is another painting type called Baltoflake. It is a glass-flake reinforced polyester coating, which provides exceptional abrasion resistance and anti-corrosion protection. It enjoys a very high resistance to mechanical damage, is ideal for splash zones and subsea structures and is excellent for offshore structures and other assets exposed to harsh marine environments.
Environmental responsibilities
There are several organisations that help promote sustainable practices and reduce environmental impact in the protective coatings industry. These include Leadership in Energy and Environmental Design (LEED) which encourages sustainable building practices, promoting coatings with minimal environmental impact, the Environmental Protection Agency (EPA) which sets regulations for VOC (Volatile Organic Compounds) emissions in coatings to protect air quality and the European Chemicals Agency (ECHA) which manages REACH (Registration, Evaluation, Authorisation and Restriction of Chemicals) regulations in the EU, which restrict harmful chemicals in coatings.
It is probably true that the most important of these organisations is LEED because it applies the international standard and codes of practice to protect the environment.
LEED is a globally-recognised certification programme developed by the US Green Building Council (USGBC). It focuses on promoting environmentally-responsible, efficient and sustainable building practices.
However, all these organisations are working on reducing hazardous emissions of Volatile Organic Compounds which impact air quality.
They also focus on coatings that use eco- friendly, non-toxic raw materials or water-based formulas, which reduce their environmental footprint.